Ensuring Safety & Reliability (and Avoiding Failure) in Mission-Critical Parts and Assemblies
There is no room for error in aerospace and defense manufacturing. When munitions or aircraft are in use, flawless performance is expected and isn’t the concern of the operator – but it is of the utmost concern for the manufacturers.
Rigorous quality control processes ensure the safety, reliability, and functionality of mission-critical parts and assemblies, and this article explains what is required to comply with stringent industry standards and establish consistency across manufacturing facilities and personnel.
Managing Quality Control in High-Stakes Aerospace and Defense Manufacturing
In aerospace and defense manufacturing, it all comes down to trust, and trust is earned by producing the highest-quality parts and assemblies that have zero defects and present no risk to the finished product.
A single faulty component can lead to catastrophic failure, resulting in loss of life and threatening national security. WIth so much on the line, aerospace and defense manufacturers rely on stringent quality control systems to minimize risk.
Numerous industry compliance standards and regulations exist for this exact reason. Aerospace and defense manufacturers can only ensure the highest quality parts and assemblies if they adhere to their applicable standards, which include:
- AS9100: AS9100 is the globally-recognized quality management standard for aerospace. It is a base standard ensuring consistent quality in design, production, and assembly processes, and companies with AS9100 certification are demonstrating their commitment to safety, reliability, and compliance, as well as deploying consistent practices across all of its facilities, departments, and personnel.
Manufacturing companies can also comply with specialized extensions of AS9100, including AS9110 for MRO and AS9120 for distributors, which each include additional requirements specific to their operations.
- NADCAP (National Aerospace and Defense Contractors Accreditation Program): NADCAP focuses on special processes, such as heat treatment, coatings, and non-destructive testing, ensuring consistent quality and compliance across the supply chain.
- ISO 9001: This standard establishes a baseline for quality management systems that can apply to any organization to demonstrate that its products or services consistently meet customer and regulatory requirements. While not specific to aerospace, this standard can be tailored to meet aerospace requirements.
- MIL-SPEC Standards: Specific to defense applications, the MIL-SPEC (or Military Specification) standards define the performance and quality requirements for military-grade components.
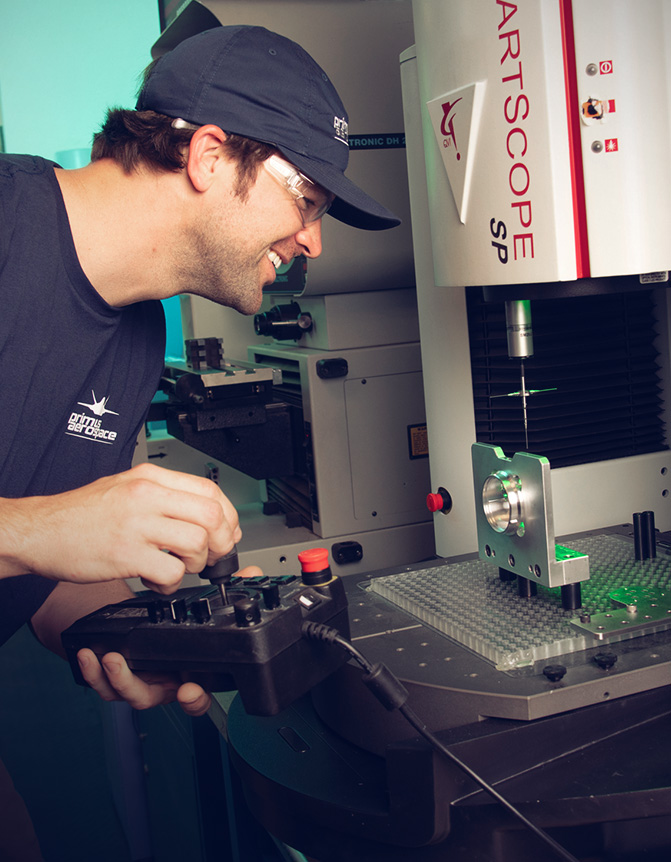
Following Through: Putting Quality Control Measures into Practice
Nothing goes untested in the aerospace and defense manufacturing industry. Testing and retesting is arguably the most critical stage of the manufacturing process as it provides proof of quality and compliance.
Some advanced testing protocols include:
- Non-Destructive Testing (NDT): Using techniques such as ultrasonic testing, radiography, and magnetic particle inspection, manufacturers can demonstrate that parts meet regulatory specifications without stress or damage.
- Environmental Stress Screening (ESS): Every part and component is subjected to different environmental stressors to simulate real-world situations and ensure performance in even the most extreme conditions.
- Lifecycle Testing: Parts and assemblies are tested for durability and reliability over simulated lifespans, ensuring they perform consistently over time.
Facility and Equipment Standards
Meeting regulatory standards and testing for quality and performance are only pieces of the overall quality control process.
The manufacturing facilities are just as critical to overall quality, and require state-of-the-art equipment and capabilities.
Cleanrooms and other controlled environments are essential to avoid contamination and ensure precision in the manufacturing process.
Machinery, such as the manufacturing and testing equipment, should also be precisely calibrated at regular intervals to guarantee accurate and consistent results regardless of the type or size of the part, or the manufacturing frequency.
Machinery Isn’t the Only Consideration for Quality
Despite how automated manufacturing has become, humans are still heavily involved – and have to be – to ensure the quality and precision required for aerospace and defense manufacturing.
Comprehensive training and education is essential for all employees to guarantee the highest level of consistency and quality across all manufacturing processes.
Your employees should be familiar with the applicable industry standards and best practices, and obtain certifications for specialized processes they are performing, such as soldering, welding, and non-destructive testing.
Also critical, your employees must be trained to identify defects or failures, and be aware of a process for reporting these issues immediately. Errors do occur, and your employees are the front line against those faulty parts or components moving on to the next phase.
Continuous Improvement: It’s All in the Name
Continuous improvement is exactly what it sounds like. There is always room for improvement and aerospace and defense manufacturers need to evolve with those industries to remain effective, safe, and successful.
Here are a few ways companies are practicing continuous improvement:
Performing Root Cause Analysis: Companies should always do a post-mortem on any defects or failures to identify and resolve the underlying cause, and better understand how to prevent it in the future.
Utilizing Feedback Loops: There is always data available from testing and field performance, which can be leveraged to enhance manufacturing processes.
Conducting Supplier Audits: Companies working with a supplier – or suppliers – should conduct regular assessments of their suppliers’ quality systems to ensure consistency across the supply chain. Your internal QC can be outstanding, but if a supplier’s is not, it will impact the ensure supply chain.
Aerospace and defense manufacturing is a highly quality-controlled industry, and the requirements and standards are clear and effective at maintaining that quality. However, understanding and implementing oversight, education, training, and best practices at your facility ensures no steps are overlooked.
Much is at stake in the mission-critical performance of aerospace and defense parts and assemblies, and not only establishing but adhering to your internal quality control processes keeps these industries moving and protects lives.Read about our commitment to quality and view a lengthy list of widely-recognized industry standards with which we are compliant.