Innovative Approaches to Developing Parts that Can Take On Everything from High Pressure to “Warp” Speeds
We talk a lot in the aerospace and defense manufacturing industry about mission-critical performance and designing parts and assemblies that can withstand even the most extreme conditions.
But what constitutes “extreme conditions”? Anyone familiar with aircraft and military-grade equipment knows there are formidable challenges out there – the high-speed dynamics of missiles and rockets, or crushing atmospheric pressures . This article will explain in depth what conditions manufacturers are testing for, and the innovations being leveraged to enhance performance, safety, and reliability.
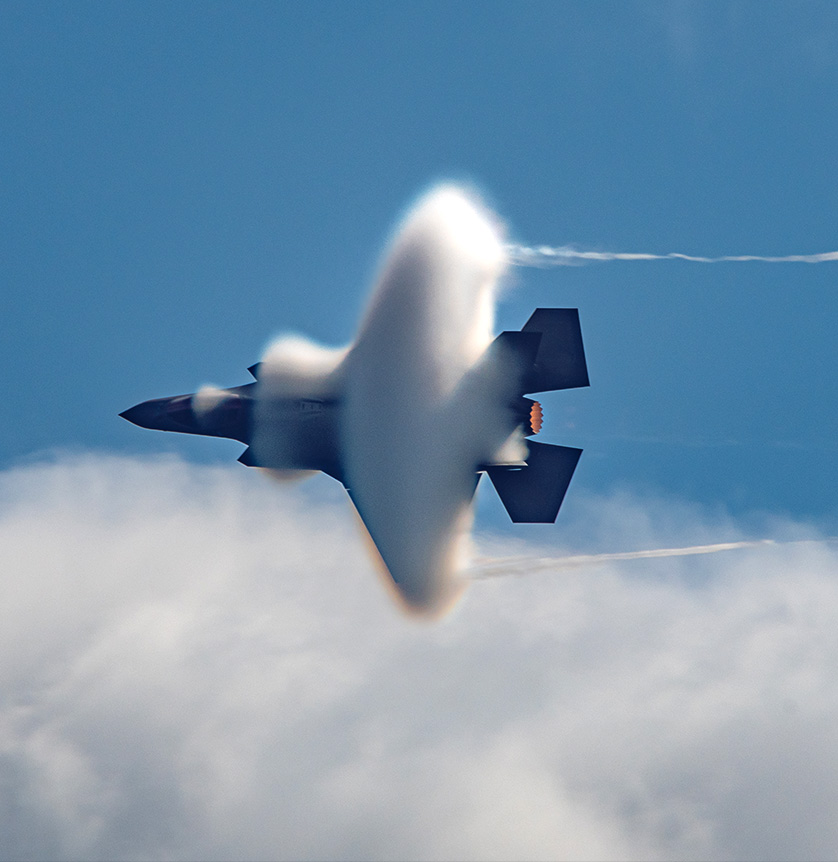
Extreme Conditions in Aerospace and Defense Operations
Unforgiving environments exist on the ground, in the air, and in space. Manufacturers must combine innovation and precision machining and fabrication capabilities to produce parts and assemblies with mission-critical performance to overcome these environmental challenges.
There are different extreme conditions for aerospace than there are for defense, and manufacturers must take all risks into account when testing performance in varying situations. Here are the most common conditions mission-critical parts must endure:
Extreme Temperature Fluctuations
Components used in rockets and spacecraft must endure extreme heat during launch and reentry, as well as the subzero temperatures of space.
Aerospace and defense manufacturers employ materials that can maintain integrity while handling massive thermal expansion and contraction
High Pressure
In applications such as deep-sea exploration and hypersonic flight, components are exposed to intense pressure that can easily deform or compromise weaker materials.
Aerospace and defense manufacturers must use the right materials to achieve an exact balance of strength and flexibility.
Corrosion and Wear
Everything from saltwater to chemical fuels to heavy wind and rain can cause corrosion and wear and tear, as material degradation can lead to catastrophic failure in mission-critical systems.
Aerospace and defense manufacturers rely on parts that can resist corrosion and wear over time despite exposure to harsh environments.
Complex Geometries and Precision
Missiles, rockets, and aircraft often require intricate designs with tight tolerances, which can be difficult to achieve with traditional manufacturing methods.
Aerospace and defense manufacturers must be proficient in:
- complex machining that can meet demands for tight tolerances
- unique and exotic alloys for high-performance applications
- engineering solutions for today’s emerging market technologies
- fabrication for any design specification
Innovative Manufacturing Techniques for Mission-Critical Performance
Now that we’ve learned about the types of extreme conditions aerospace and defense products are up against, let’s look at the innovations driving manufacturing.
Advanced Materials: Aerospace applications in particular demand materials that are at once strong and lightweight, delivering high performance while maximizing fuel efficiency and payload capacity.
There are three main categories of advanced materials that balance strength and weight while offering other benefits like corrosion resistance and formability.
- Superalloys: High-performance alloys such as Inconel and titanium are widely used for their ability to maintain strength at high temperatures and resist corrosion.
- Composite Materials: Carbon fiber-reinforced polymers (CFRPs) offer high strength-to-weight ratios, making them ideal for lightweight structural components.
- Ceramic Matrix Composites (CMCs): These materials are increasingly used in jet engines and hypersonic applications for their ability to withstand extreme heat.
Additive Manufacturing (3D Printing): Additive manufacturing enables the creation of complex geometries and reduces material waste.
3D-printing allows manufacturers to customize parts and assemblies to meet specific mission requirements, and to consolidate multiple components into a single part, reducing potential failure points.
Simulation and Modeling: Advanced computational tools create simulations of real-world conditions during the design phase, so engineers can more accurately predict how materials and components will perform under stress.
These simulations also inform how engineers can optimize designs for thermal, pressure, and aerodynamic conditions.
Surface Treatments and Coatings: Specialized coatings enhance resistance to corrosion, wear, and thermal stress. These treatments and coatings can include:
- Thermal Barrier Coating (TBC), which is used across industries, including aerospace, to protect surfaces from extreme heat. For example, a thermal barrier coating would be applied to jet engine turbine blades to protect them from the extreme heat of the engine.
- Anti-corrosion coatings, which extend the life of components exposed to harsh environments. For example, anti-corrosion coatings would be applied to a naval ship to protect it from degradation due to saltwater exposure, or to a military vehicle to prevent rust caused by hot, humid, or harsh terrain and weather.
Precision Manufacturing Techniques: Computer Numerical Control (CNC) machining and other precision machining services like electron beam welding can achieve even the most difficult tolerances and designs, as well as repeatability in production. These techniques are essential for components that must fit seamlessly into larger assemblies.
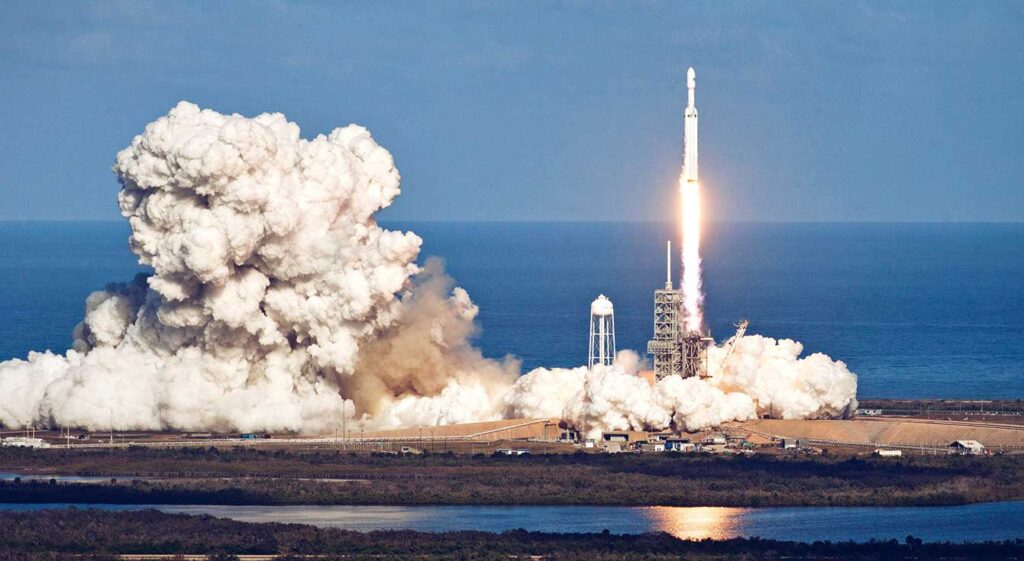
The Future of Extreme Condition Manufacturing
The aerospace and defense industry continues to push boundaries, with emerging innovations poised to redefine manufacturing, especially as it pertains to mission-critical performance in extreme conditions.
Here are just a few emerging technologies that are taking shape right now.
- Hypersonic Technologies
Hypersonic flight is a snappier way to describe flying through the atmosphere at Mach 5 speed or higher – which is 5 times the speed of sound. While hyperonic flight has been achieved several times, even as far back as 1961, it is becoming a new frontier for high-speed air travel that could impact mankind and how we fly.
Manufacturers are readily developing materials and designs that can withstand the intense heat and pressures generated at these extreme speeds.
- Smart Materials
Self-healing materials and shape-memory alloys have the potential to enhance reliability and reduce maintenance needs in critical systems.
Beyond the obvious cost-savings, these smart materials will allow for greater adaptability and faster, more localized repair, minimizing downtime, equipment shortages, and safety risks.
- AI and Machine Learning
AI and machine learning are playing a role in almost every aspect of our lives these days, and the aerospace and defense industries are no exception.
AI-driven design tools are enabling faster component prototyping and optimization, while machine learning algorithms can predict wear and failure, improving maintenance schedules and minimizing downtime.
- Sustainable Manufacturing
The aerospace and defense industries have been striving for some time toward greater sustainability, and now, innovations in recycling for composite materials and eco-friendly processes are gaining popularity and helping transform these industries to adopt more planet-positive practices.
Mission-critical performance relies on the ability of parts and assemblies to withstand extreme conditions.
Aerospace and defense manufacturers are blending ingenuity, precision, and cutting-edge technology with advanced materials, additive manufacturing, and innovative engineering techniques to rise to the challenge.
As new technologies emerge, the aerospace and defense industries will continue to evolve, unlocking even greater capabilities and pushing the limits of what mission-critical performance looks like in the most extreme environments.
Learn more about our precision machining capabilities for complex parts and assemblies.