What is honing?
Honing is mechanical finishing process used by aerospace machine shops and outside processors to achieve a precision surface on a metal part. Hones use superabrasives, also known as a honing stone, to a specific finish over the entirety of a metal surface. These abrasive stones, configured on a tool assembly, provide consistent abrasion to the work piece. Honing is also called bore finishing, as it is most commonly conducted on cylindrical surfaces as a finishing technique.
The honing process is conducted with honing stones or with wire brushes that provide a very specific level of abrasion to the metal work piece. Honing stones are generally an aluminum oxide or silicon carbide abrasive material, which is bonded with resin.
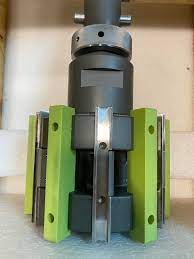
Where did honing originate?
Modern honing techniques date back to the 1940’s with the foundation of Superior Hone in Elkhart, IN. The original intent of mechanical honing equipment was to deglaze automotive cylinder bores, but as the technique was perfected, additional applications presented themselves.
What are common types of mechanical honing equipment?
- Vertical hone – Vertical honing machines use a drive shaft that is oriented vertically and moves along the work piece in an up and down motion. An example of a vertical hone would be the Ohio Tool Works PowerHone. Primus Aerospace utilizes an onsite Barnes 3010 honer to provide in-house honing as part of a turn-key manufacturing solution.
- Horizontal hone – Horizontal honing machines are laid out across a floor footprint where the drive shaft moves forward and backward through a work piece. An example of a horizontal hone would be the Ohio Tool Works VersaHone. Sunnen is another manufacturer that specializes in honing equipment for vehicle engine applications.
Honing machines also differ in their capability to handle various bore diameters and part lengths/heights. Primus’s honing capability specializes in parts that are ideally used for aerospace hydraulic reservoirs and cylinders.
What is single pass vs multi pass honing?
Most honing applications take multiple passes (known as stroke honing) to achieve the desired surface finish and depth. Specific applications, such as engine crank arms or cam bores, require single pass honing to ideal performance.
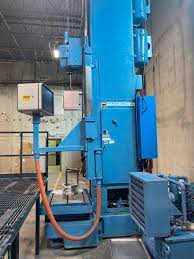
Why is honing performed in aerospace and defense applications?
Honing allows a manufacturer to achieve a precision surface finish that is critical for some aerospace applications, such as hydraulic systems. Aircraft manufacturers and tier one suppliers design hydraulic systems as part of the control system. In addition to aerospace control systems, honed aerospace parts are in pumps, valve sleeves, accumulators, fuse pins, and landing gear components. Honed parts reduce friction, remove burrs, and increase equipment dependability over its service life. In specific aerospace applications, the inner bores of gears or weapon barrels are honed.
What is the advantage of a machine shop that has integrated honing?
While many aerospace and defense machine shops offer honing, very few have the honing capability inside their company. When aerospace machine shops produce a part, the production sequence may require additional capabilities (such as honing, painting, precision grinding) to meet the customer’s build-to-print requirements. When those capabilities aren’t organic to the part manufacturer, they will utilize outside processors (OP Houses) to perform specialized work. More sophisticated machine shops have additional value added services inside the company, which allows them to expedite priority parts and ensures adherence to a single quality management system (QMS), generally at the AS9100 level. Primus Aerospace constantly adds additional capabilities, such as wire EDM, honing, and grinding, to its services to provide turn-key manufacturing solutions for aerospace and defense parts.
Does Primus offer honing to aerospace & defense customers?
Yes! Primus Aerospace offers honing as a valued added service to its build-to-print aerospace part production service. Primus does not offer standalone honing as a separate service to other local machine shops, but could in the future.