The Advantages of Lean Six Sigma in Aerospace and Defense Manufacturing
At its core, Lean Six Sigma in aerospace and defense manufacturing exists to improve organizational performance. Combining the principles of Lean manufacturing and Six Sigma helps organizations be more effective in approaches to process improvements – and in this industry, there is a continuing focus on evolving how we get the job done.
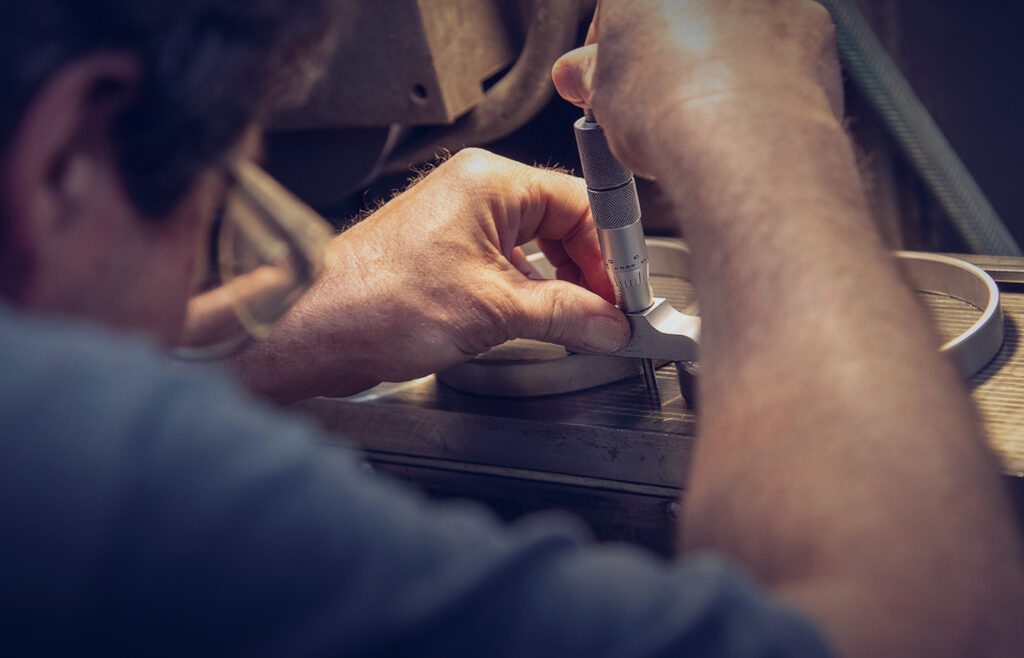
Managing the Pressures of Production with a Lean Approach
Lean practices aim to eliminate waste, reduce variation in processes, improve quality, and enhance customer satisfaction, and in aerospace and defense these practices reinforce a commitment to quality, delivery, and cost.
Pressures to optimize production schedules and reduce supply chain costs are only increasing, and manufacturers are looking for ways to remain competitive without cutting corners – especially because there are very few corners to cut.
Lean manufacturing practices allow companies to focus on continuous improvement, waste reduction, and process efficiency with the goal of enhancing the delivery of exceptional quality while reducing overall costs. At Primus, this mindset is built into everything we do through Lean Six Sigma and our own Primus Production System, an integrated approach that aligns people, processes, and technology. Our adoption of Lean principles has helped drive value across the board.
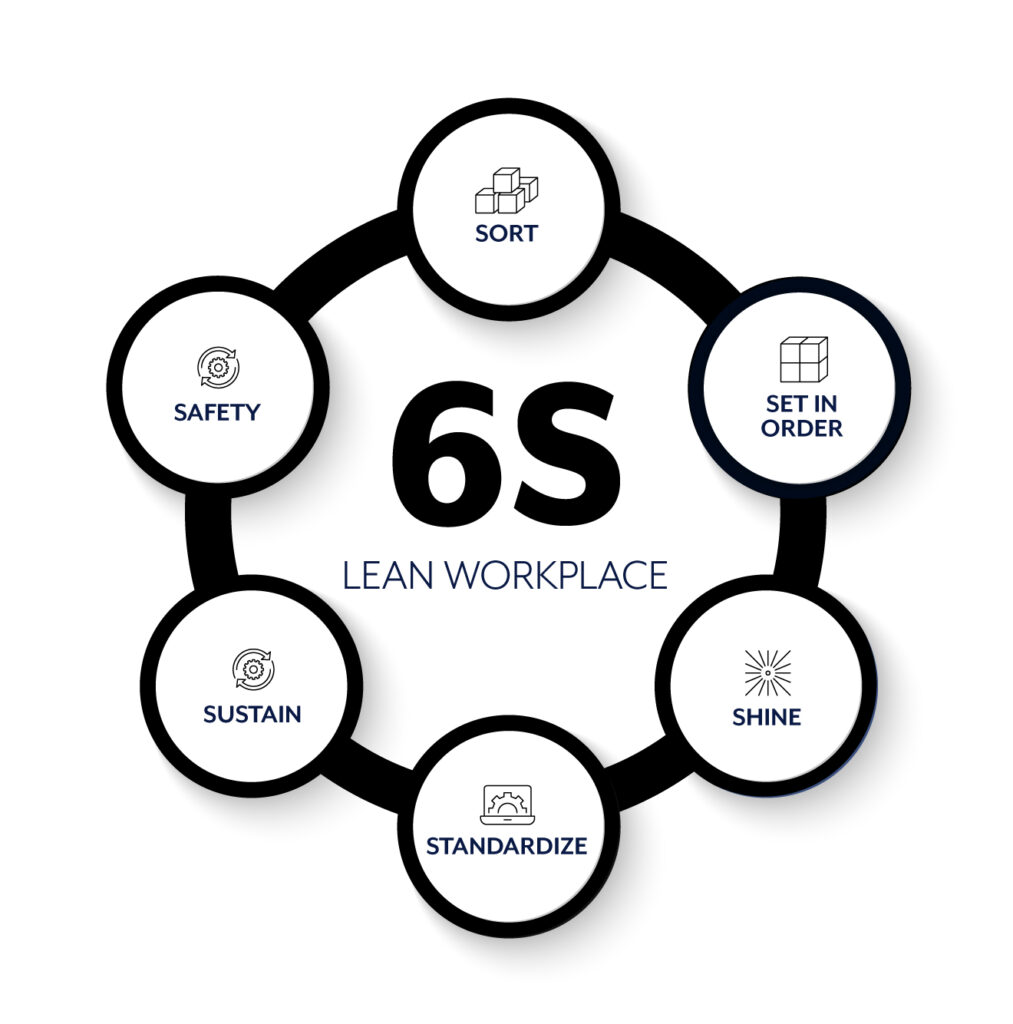
Lean Manufacturing: A Strategic Imperative in Aerospace & Defense
Demands for tight tolerances, rigorous quality standards, and adherence to performance requirements for mission-critical parts and assemblies leaves no room for error in aerospace and defense manufacturing.
At the same time, demands for greater efficiency, reduced lead times, and lower costs challenge the way we approach manufacturing.
Lean manufacturing provides a framework to meet both goals.
By systematically identifying and eliminating non-value-added activities – commonly referred to as “waste” – Lean practices improve process flow, reduce production variability, and maximize the use of resources. These improvements are especially important for aerospace OEMs and Tier 1 suppliers who rely on precise, dependable partners to deliver components on time and on spec.
The Primus Production System: Lean in Action
We built a fully integrated operating model around Lean practices. The Primus Production System (PPS) is our in-house approach to Lean manufacturing, combining advanced technologies, skilled personnel, and disciplined processes to drive measurable performance improvements.
Built on the foundation of Lean Six Sigma, the PPS emphasizes:
- Standardized work to minimize variation
- Visual management systems for real-time decision making
- Cellular manufacturing to reduce setup times and streamline workflows
- Continuous improvement (Kaizen) initiatives led by cross-functional teams
- Advanced machining and automation technologies to increase throughput without sacrificing precision
As a result, we’ve achieved a more agile, responsive, and efficient production environment – one that enables us to meet the rigorous demands of aerospace and defense customers while maintaining the highest standards of quality.
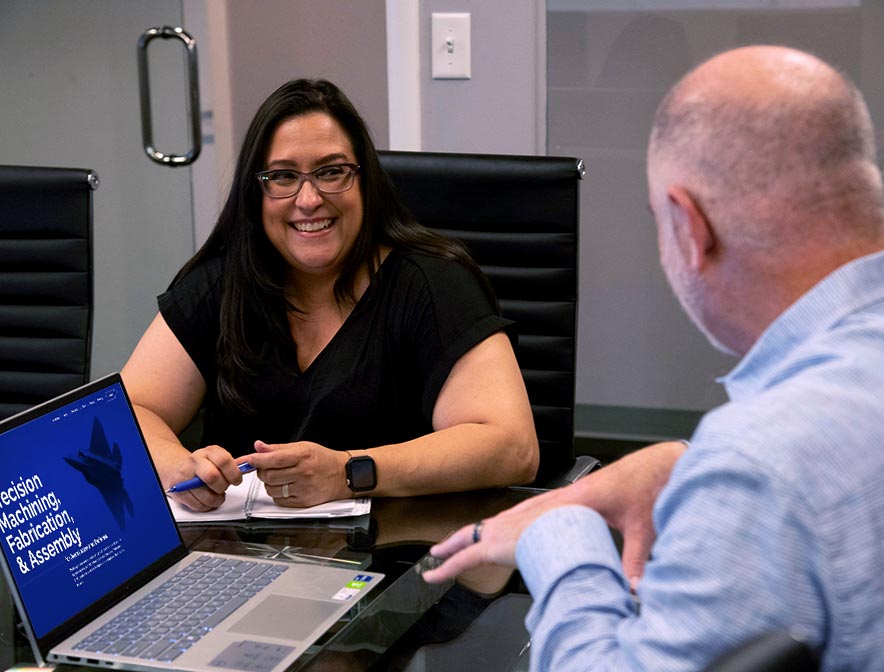
Reconciling the Cost–Quality Challenge
A common misconception about cost-cutting in manufacturing is that it inevitably impacts product quality. However, when implemented correctly using Lean manufacturing practices, cost-cutting actually does the opposite.
By designing out inefficiencies and standardizing best practices, Lean methods help manufacturers consistently meet quality benchmarks while reducing the cost of poor quality (CoPQ), including scrap, rework, and delays. For industries like aerospace and defense, where the cost of a single defect can be enormous, this balance is critical.
Other positive outcomes to the application of Lean manufacturing include:
- Lowering inventory carrying costs
- Improving supplier coordination
- Shortening production lead times, giving manufacturers the ability to respond quickly to changes in demand or program schedules without compromising delivery.
Lean Strategies that Strengthen the Supply Chain
Lean isn’t just a production philosophy – it’s a strategic supply chain advantage. When every link in the value chain is optimized for efficiency and performance, you create a more reliable, cost-effective, and agile operation.
For Primus, these supply chain advantages include:
- Partnering more closely with OEMs and Tier 1 suppliers
- Collaborating on DFM/DFA (design for manufacturability/assembly) early in the product lifecycle
- Accelerating time to production without sacrificing attention to detail
- Delivering flight- and mission-critical parts with consistent performance
Whether we’re machining complex missile components, producing hydraulic actuators, or assembling avionics enclosures, our Lean manufacturing culture ensures that our customers receive the highest quality products on time and within budget.
Lean Is a Competitive Advantage
If you aren’t yet doing so, align your operations around Lean principles and consider deploying a proprietary system like the Primus Production System to tailor specific benefits to your unique environment.
Lean thinking helps manufacturers reduce costs, eliminate inefficiencies, and maintain an unwavering commitment to quality. At Primus, Lean is how we build better parts—and better partnerships.