What is mill turning?
Mill turning is the CNC machining technique of utilizing a single machine to perform both milling and turning (lathe) operations to produce a part. The use of a single machine to perform both types of cutting operations can simplify the production flow of a part through a CNC machine shop. It can also increase the repeatability as the part does not need to be fixtured multiple times. Mill turning can be done on multi axis (e.g., 5 Axis Mill) as well as a lathe with live tooling.
When is mill turning used?
Mill turning is great for cylindrical parts that have non-cylindrical features (e.g., posts, studs, through holes) and need to be produced at a high rate. Utilizing a CNC mill turn machine, allows contract manufacturer to reduce the number of operations / separate CNC machines needed, thereby increasing capacity and production rate. Many mill turn parts exist on defense ordnance and fuzing programs, due to their overall cylindrical nature and relatively high production rate requirements from the US Department of Defense.
What are considerations for production mill turn parts?
- CNC Programming – Programming a mill turned part takes an experienced mill turn programmer as well as specialized CAM software. Many programmers utilize the Mastercam Mill Turn.
- package to coordinate and simulate the multiple cutting steps as well as the hand over of parts to a sub-spindle. These types of contract manufacturing jobs often require high production rates, making cycle time a premium. CNC programmers must be able to optimize the CNC program to maximize throughput on the machine.
- CNC Mill Turn Machine – mill turn machines are specialized pieces of equipment that have the ability to both cut while the work is turning (lathe / turning) as well as move cutting tools around the work (mill). Most modern CNC manufactures produce machines capable of mill turn operations.
- Multiple spindle / turret (automation) – many mill turn machines feature multiple spindles and/or turrets. This allows the CNC machine to conduct more cutting paths in a single CNC program. Sub-spindles can be used to cut features on the “backside” of a part while a second turret allows simultaneous cutting operations.
- CNC Machinists – Running production mill turned parts takes a specialized machinist as they must think in both milling and turning (lathe) operations. Check our open positions for job openings for CNC Mill Turning Machinists.
- Inspection Capabilities – With high rates of production for complicated parts, mill turn production lines require smart inspection support. This can translate into well through out in-process inspection checks (IPICs) as well as end-of-line Qa lot inspections. Leveraging automated inspection equipment (e.g., CMM, Smart Scope) is essential to detecting deviation from nominal early and making tool offsets before they become a problem.
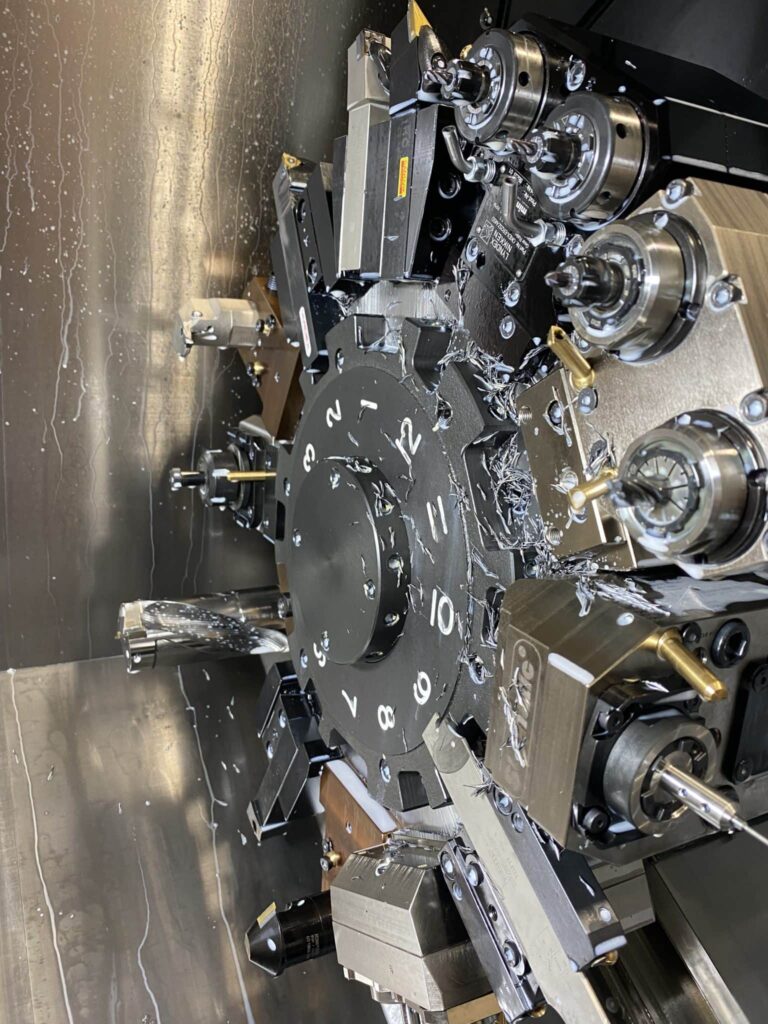
What are examples of mill turn CNC machines?
CNC Mill Turn machines are also known as multifunctional mill turn machines or lathes with live tooling.
- DMG Mori – NLX 2500, NLX 3000, NTX 1000 – 3000, CTX 800 – 3000, CLX 450
- Doosan – Puma MX, Puma SNX
- Mazak – QUICK TURN 100MS, Qt-EZ 10, HQR-250
- Haas – VMT-750
Primus’s capacity to produce mill turn parts for defense applications
Primus Aerospace maintains an Ordnance and Fuzing Cell that supports the high rate production of mill turned parts for multiple US Prime DoD customers. This team has the necessary equipment, training, and expertise to reliably produce mill turned parts for aerospace and defense applications. Additionally, our Quality Assurance (Qa) department also has the expertise and equipment needed to support the high rate production of this cell. They are familiar with the features found on mill turned parts and can quickly problem solve when a deviation is detected.