Strategies for Ensuring the Highest Quality When There’s No Room for Error
Tight tolerance machining is why aircraft, missiles, rockets, munitions, and other aerospace and defense applications can perform and withstand the exceptional stress placed on them during operation.
These mission-critical applications must meet stringent regulations and exacting specifications to tolerate extreme conditions like temperature fluctuations, corrosion and wear, and high or low pressure. Aerospace and defense manufacturers are tasked with satisfying tight tolerances while using exotic and complex materials, which raises the stakes and removes any margin of error; even a minuscule deviation can compromise performance, safety, or mission success.
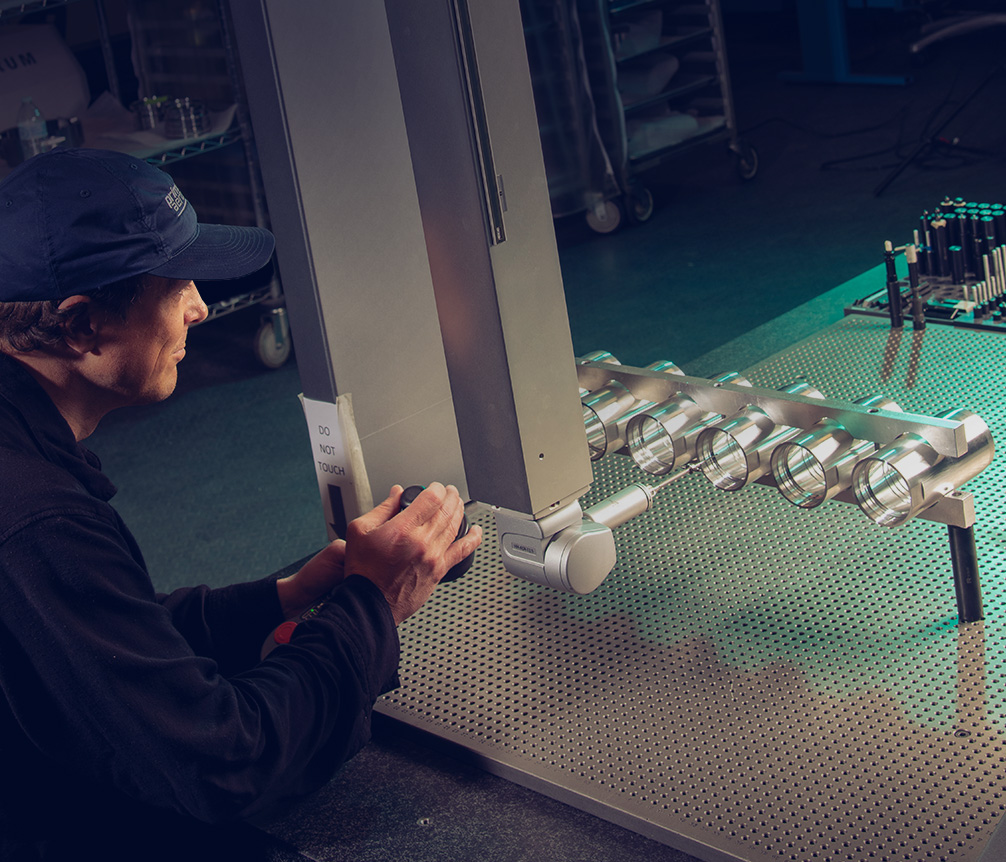
Tight Tolerance Machining Measures Precision by the Micron
Because aerospace and defense applications have to meet compliance regulations and safety standards for mission-critical performance, tight tolerance machining ensures their parts function as intended.
For example, the parts that make up aircraft propulsion systems or avionics must fit and perform flawlessly to avoid catastrophic failure.
Read more: Manufacturing for Extreme Conditions
Manufacturers have several considerations when working with tight tolerances:
Process Control:
There must be exceptional control over manufacturing processes to achieve micrometer-level tolerances. Any variability in tooling, environmental conditions, and even machine calibration can lead to deviations.
Inspection and Validation:
Advanced inspection technologies and techniques are required to verify that parts meet tight tolerances. Conventional tools often lack the necessary precision, necessitating investments in state-of-the-art metrology equipment.
Costs and Lead Times:
The precision required in aerospace and defense manufacturing can increase costs and extend lead times, particularly when rework is necessary due to non-conformance.
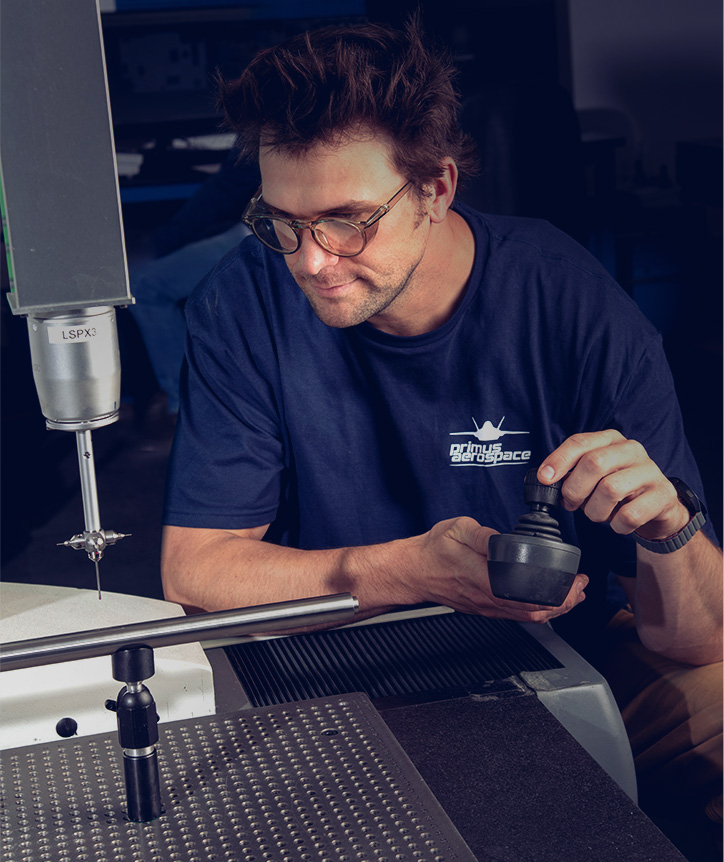
The Delicate Balance of Tight Tolerance Machining With Exotic Materials
Exotic and complex materials, such as titanium alloys, carbon composites, Inconel, and other superalloys, are chosen for their unique properties—such as high strength-to-weight ratios, resistance to corrosion, and thermal stability—but they can be notoriously difficult to machine and process, especially when manufacturing for tight tolerances.
Exotic materials often have unique properties that can make machining and forming more challenging.
For example, titanium is an excellent material for aerospace applications because it offers lightweight but high strength, corrosion resistance, high fatigue strength, strong temperature tolerance, and design flexibility. However, titanium also has poor thermal conductivity, which can lead to tool wear. Using this material in tight tolerance machining requires specialized machines and exacting parameters to ensure precision and reduce wear and tear.
When balancing tight tolerance machining and exotic materials, the following strategies can help ensure the highest quality:
- Use Advanced Equipment and Technology
Modern manufacturing demands cutting-edge machinery and tools capable of maintaining tight tolerances. These include multi-axis CNC machines, additive manufacturing for complex geometries, and high-precision grinders.
Ensure consistent performance by pairing this equipment with real-time monitoring systems.
- Optimize Process Parameters
Implement finely-tuned parameters to reduce tool wear and ensure precision while machining exotic materials. These parameters can include:
- Cutting speeds and feeds: Specified for each material’s unique properties.
- Coolant strategies: Manage heat buildup and prevent thermal distortion.
- Tool selection: Coated or specialized tools designed for exotic materials.
- Implement a Rigorous Quality Management System (QMS)
A robust quality management system complies with industry regulations and standards and is complimented by quality manufacturing processes, sustainable practices, and high supplier quality standards.
Important components of a QMS include:
- Documented processes and procedures.
- Regular audits and assessments.
- Root cause analysis for addressing deviations.
- Climate controlled laboratories.
Read more: Quality Control in Aerospace and Defense Manufacturing.
- Leverage Advanced Inspection Techniques
Highly-precise inspection is critical when tolerances are tight. Techniques such as coordinate measuring machines (CMMs), laser scanning, and non-destructive testing (NDT) provide the precision needed to verify conformance with measurement capability to less than 1 micron. These technologies also enable comprehensive data collection for traceability and analysis.
- Adopt Lean Six Sigma Practices
Lean Six Sigma principles help manufacturers minimize waste and variability, which is particularly important for processes involving exotic materials where inefficiencies can lead to significant cost overruns. Techniques such as statistical process control (SPC) and failure mode and effects analysis (FMEA) can identify and mitigate risks early.
- Train and Empower Your Workforce
Even with the best tools and technologies, skilled personnel are the backbone of high-quality manufacturing. Ongoing training programs ensure that operators and engineers stay current with the latest techniques, tools, and materials.
- Collaborate with Trusted Partners
Supplier and partner relationships governed by quality standards enable manufacturers to source raw materials, components, and specialized services from trusted entities. Select partners who share a commitment to quality and understand the unique demands of aerospace and defense manufacturing.
The Technology-Process-Quality Combination
Advanced technology, process optimization, and the highest quality are an essential combination for tight tolerance machining with complex and exotic materials.
Mastering these strategies ensures parts and assemblies meet even the most stringent industry standards for quality while delivering safety and reliability of mission- and flight-critical applications.
Get your next project off the ground with a manufacturing partner that specializes in working with tight tolerances and exotic materials. See how Primus delivers unparalleled precision and quality.